Woofsnaval: an outrigger canoe
The weather was nice and I was out doodling around with Griswold, which led to thoughts of improving the sailing rig. It reached the point where every component had a plan for improvement drifting in my head. The one stumbling block my mind's eye couldn't get over was how to improve the connection of the outrigger booms to the canoe hull without modifying the hull. The boat-fever was starting to rage, as I kept hitting this same wall, over and over agian.
Hey jezra, if your are going to replace just about everything, why not just make a whole boat? …and design it specifically to have an outrigger, and maximized cockpit space?
don't mind if I do!
What I came up with, is a 4 meter outrigger canoe; made from 6mm ACX plywood and 3.5cm rigid foam insulation from the hardware store, pine and oak from a local mill, and some of this and a few bits of that. Woofsnaval because I took a picture of an insect larvae. More on that later.
Step 0: make a plan, and write it down. It's all fine and dandy to want to make a boat, and having a plan is a great way to do that, but hot damn, having guiding material that can be referenced over and over sure does keep the build amoving.
cool, let's get crackin
Inkscape a design
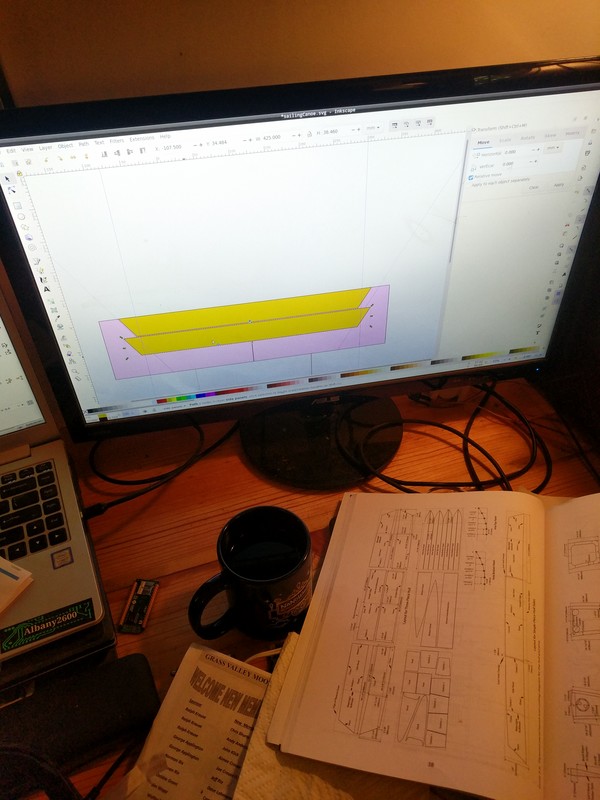
In Inkscape, the sides of the hull were drawn to scale along with 122x244cm sheets to represent the standard size of plywood available at the hardware store. Now the shapes need to transfered to cardboard.
1:10 Model
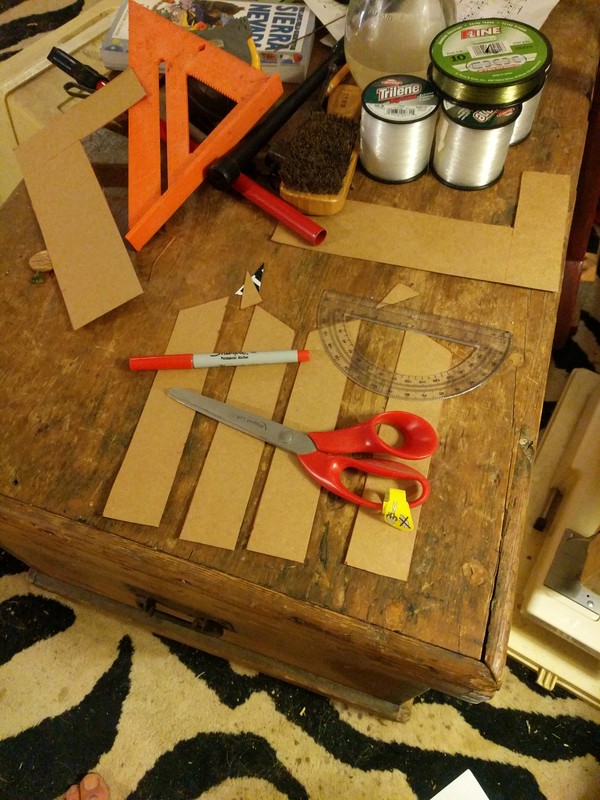
3D
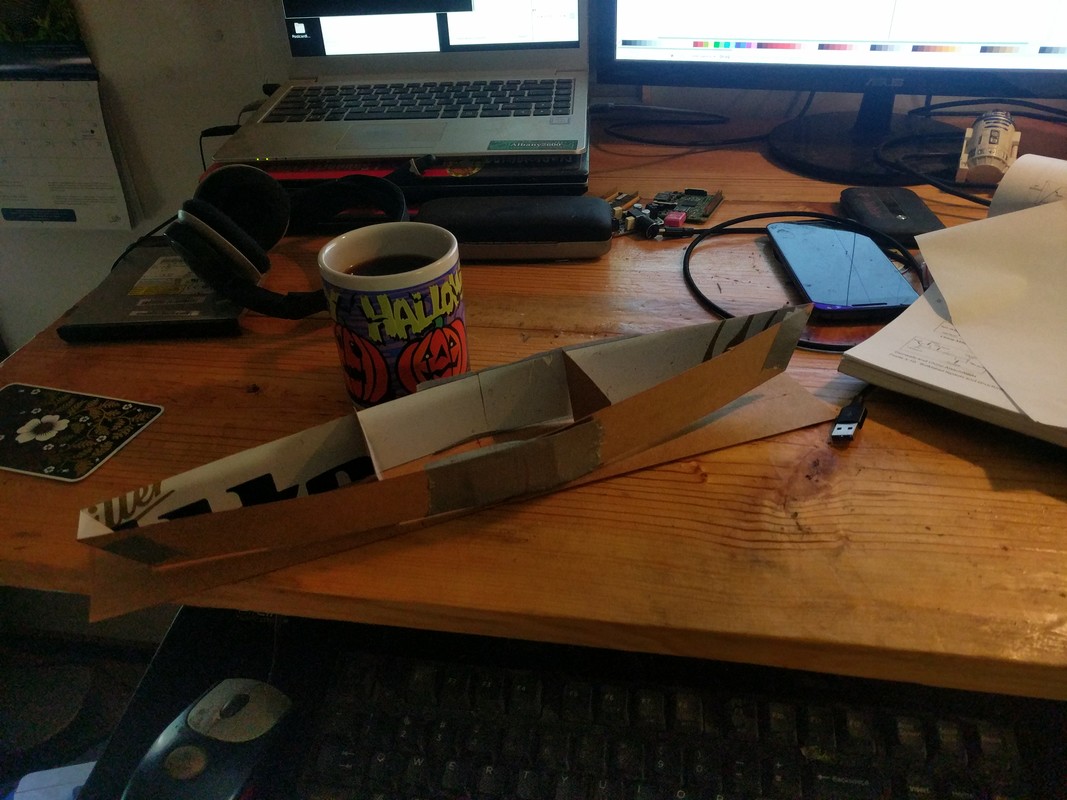
Making panels for the 1:1 model :)
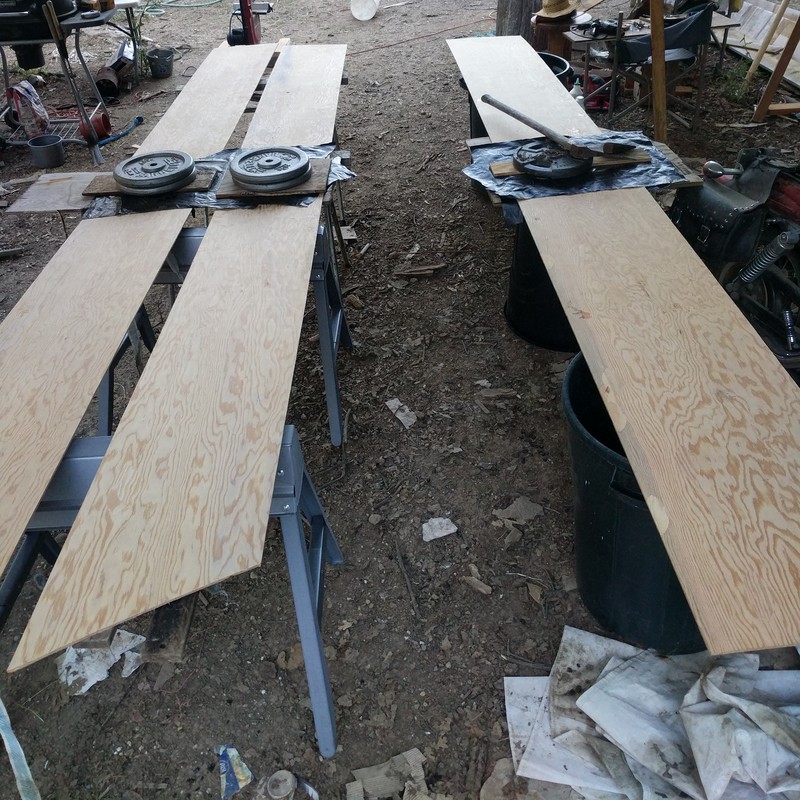
Going 3D!
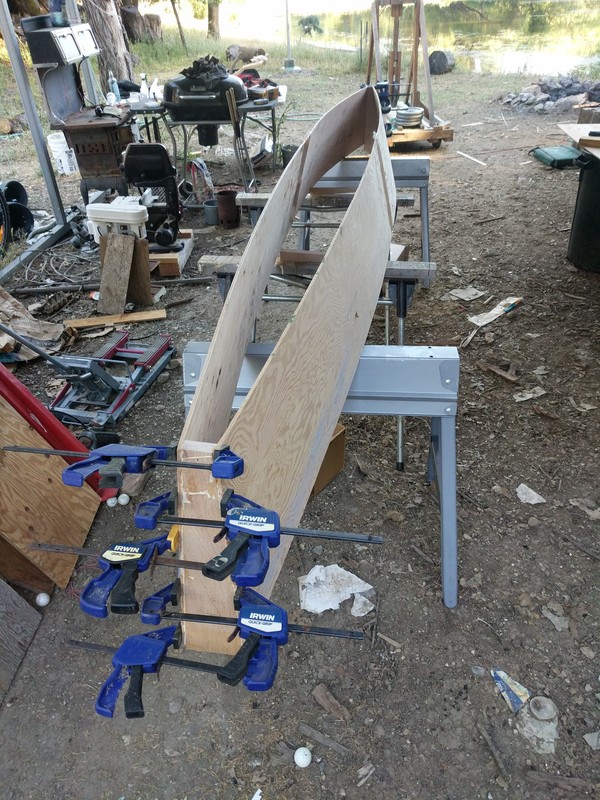
Tack the bottom in place
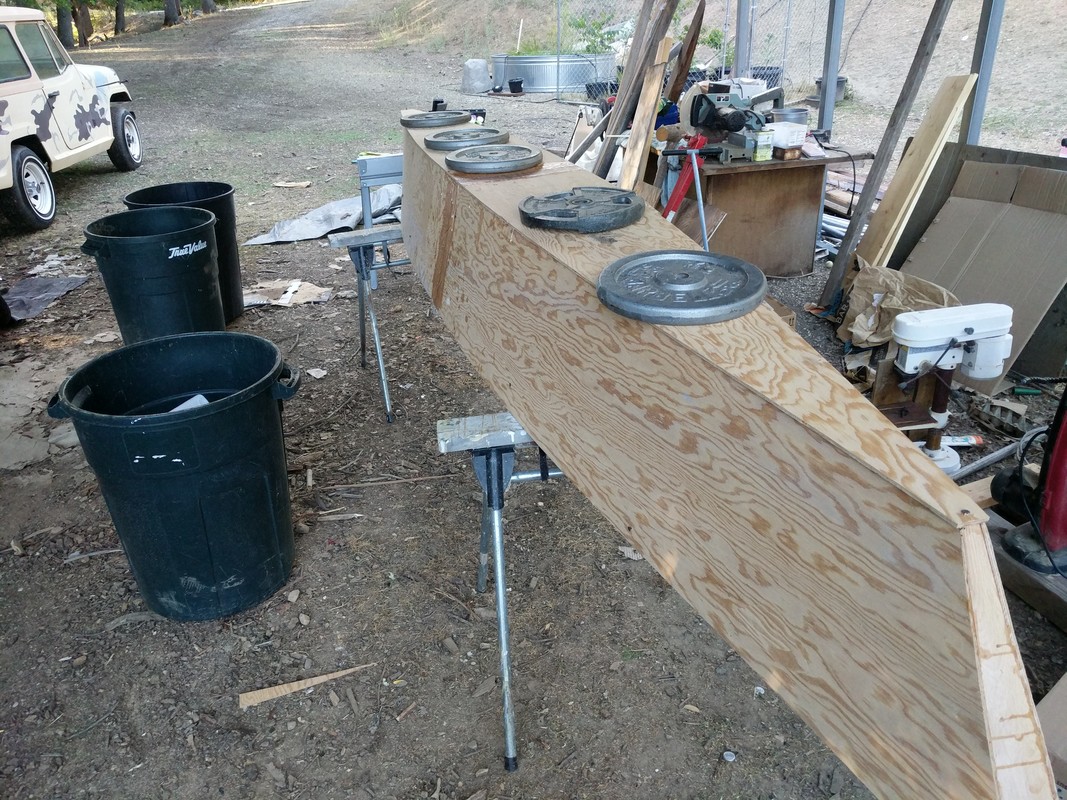
Adding bulkheads
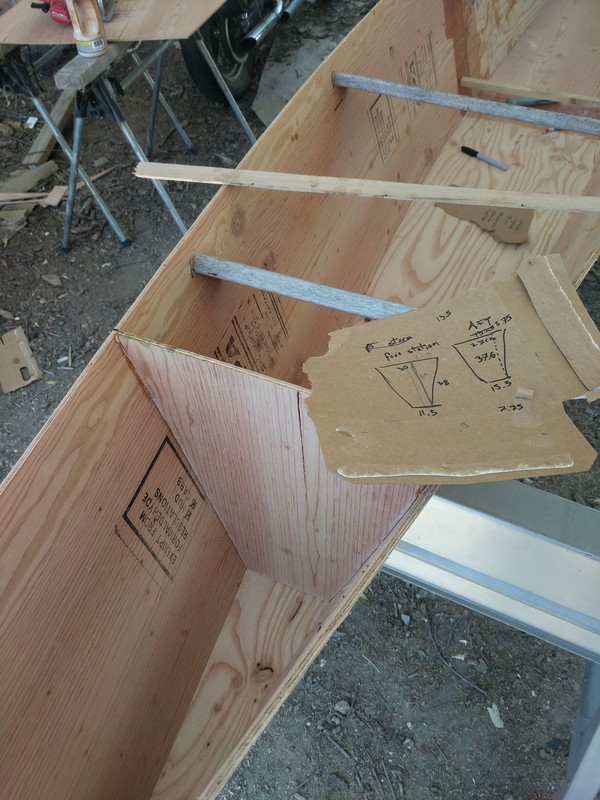
Uh... where is the fillet pic?
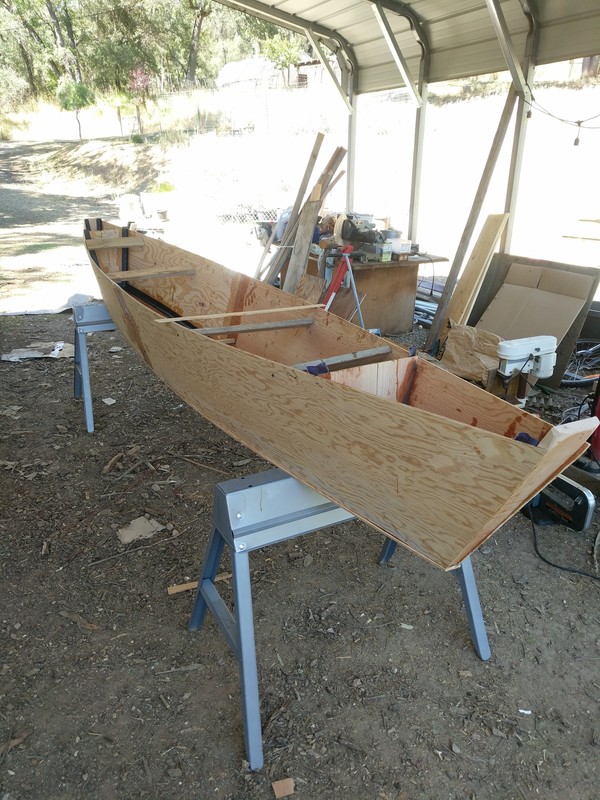
That shape though... dreamy
Ripping Gunwales
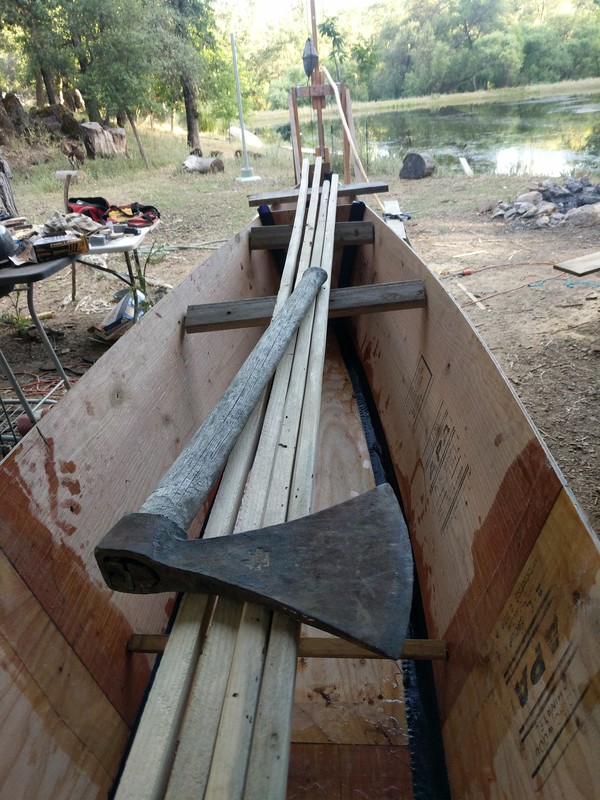
Make hella clips from a plastic pipe
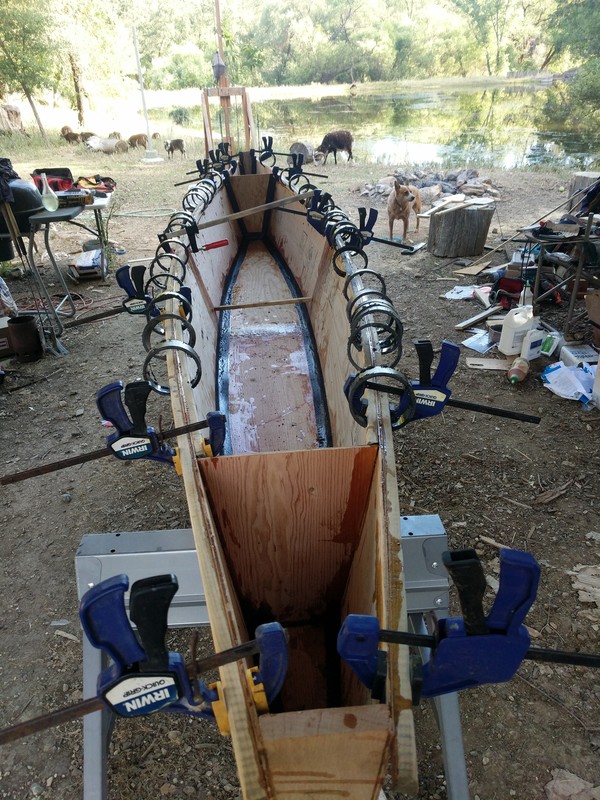
New tool
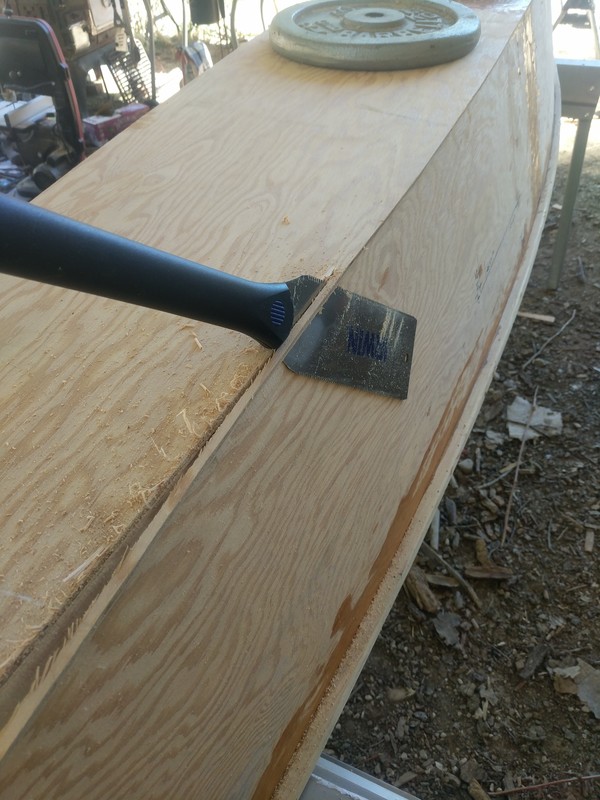
Woofsnaval
What is it? Beats me, I didn't come up with the name. Wikipedia did.
Once or twice a year, for the past few years, I have had the pleasure of encountered the California firefly.
Although it is a firefly, only the larvae are bioluminescent. To me, it is a treat
to behold and a challenge to photograph. On the night of California Independence Day, I was out in the dark, laying on
some rocks, trying to take a picture of a 5mm bug with a glowing tail that turns off when
it sees light of any kind. A picture of the glow was not captured; but a decent enough picture of the larvae was.
When I looked up the insect on Wikipedia, there was very little information, and no image. What a shame. Hold on a tick, didn't I just take a decent picture of the larvae? Yes I did, and if you ask me, the pic I took is better than the non-existent image on wikipedia, so I decided to add my picture to the article.
In order to upload an image directly to an article, one needs a Wikipedia account that is older than 4 days, and the editor needs to have made at least 10 edits to wikipedia. To get around this limitation, one can upload an image to Wikimedia Commons, and then edit a Wikipedia article to include the image. To do any of that, one first needs a Wikipedia account, and the account creation process includes filling out a CAPTCHA.
Anyway, the Wikipedia article for Ellychnia Californica now has an image :)
My Wikipedia CAPTCHA
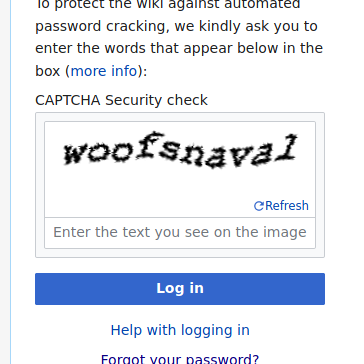
Epoxy and fiberglass
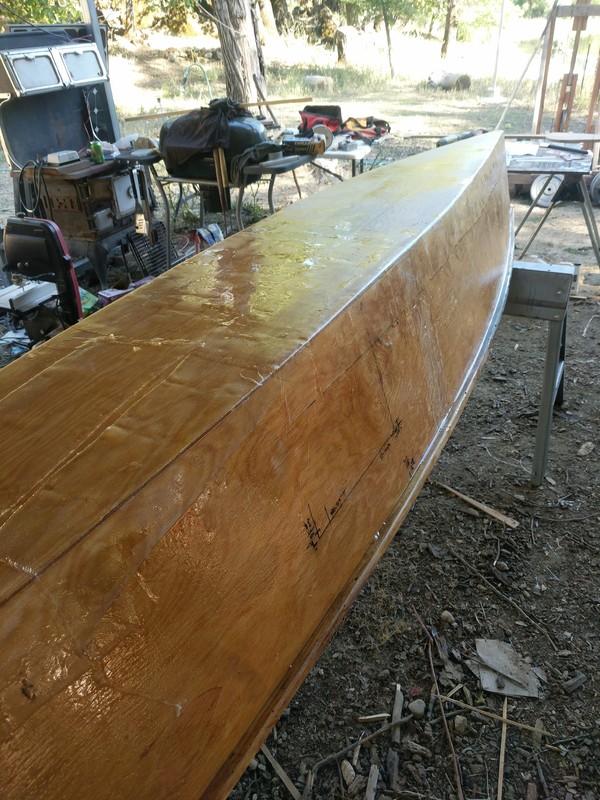
Outrigger design
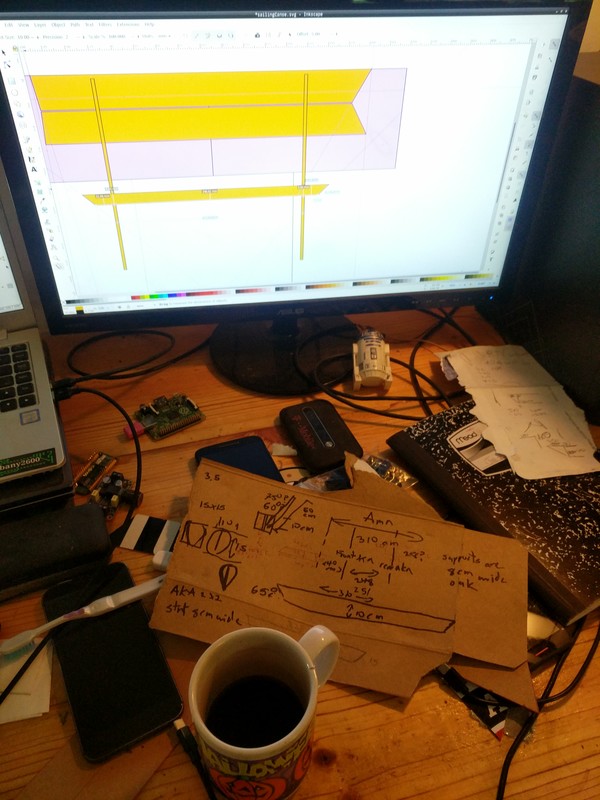
Seat supports
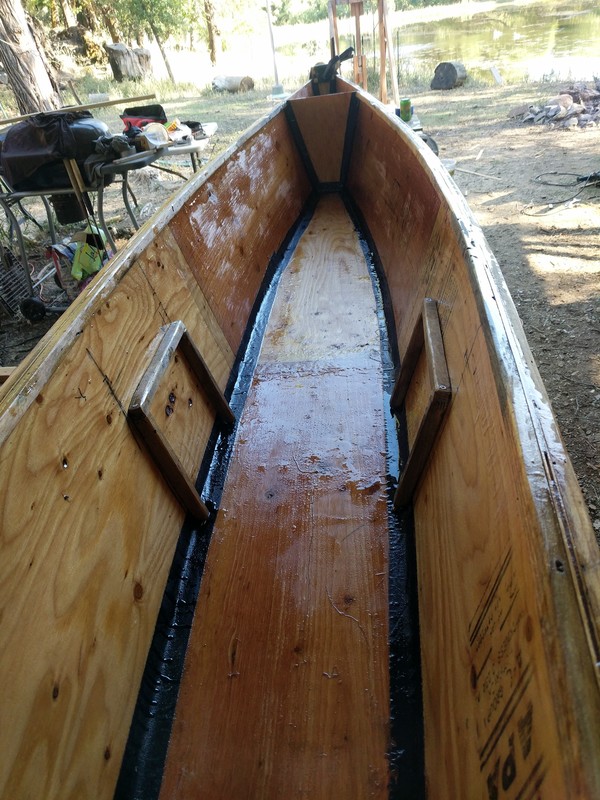
Two pieces of ply for the stringer
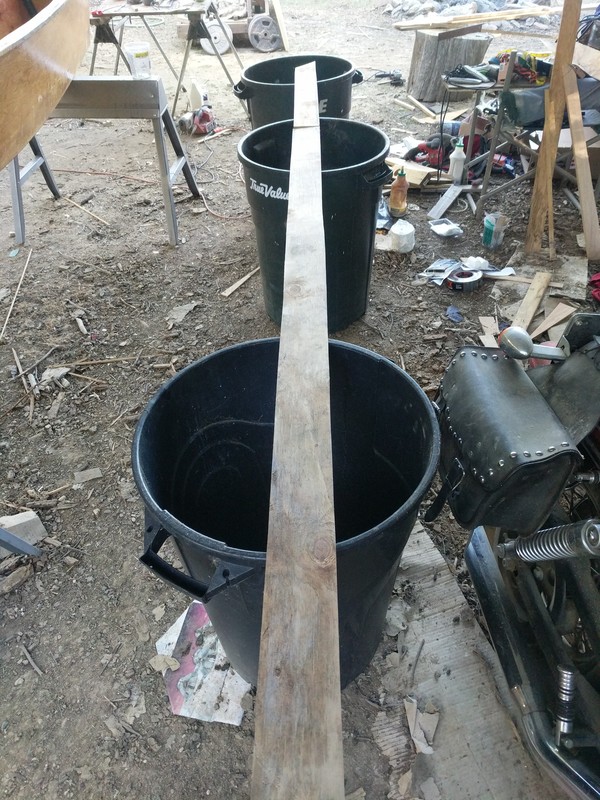
Foam and struts
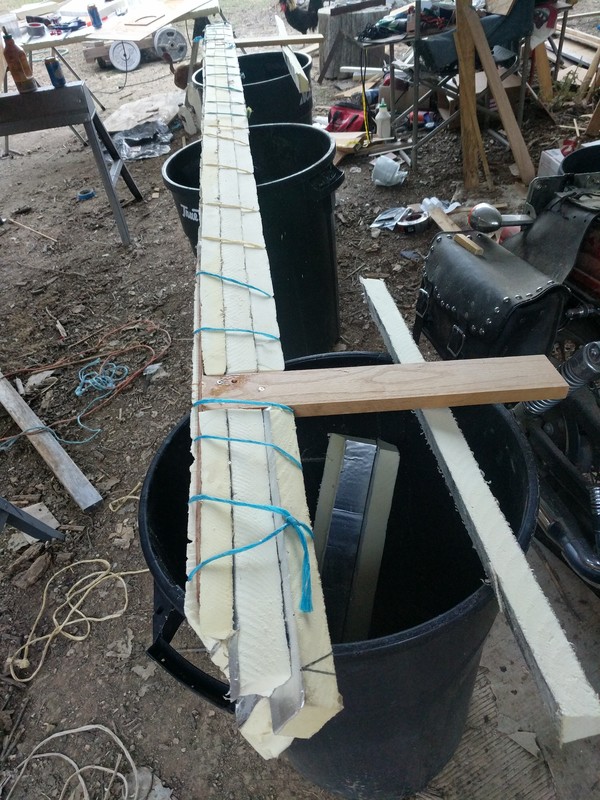
Wooweee, it floats
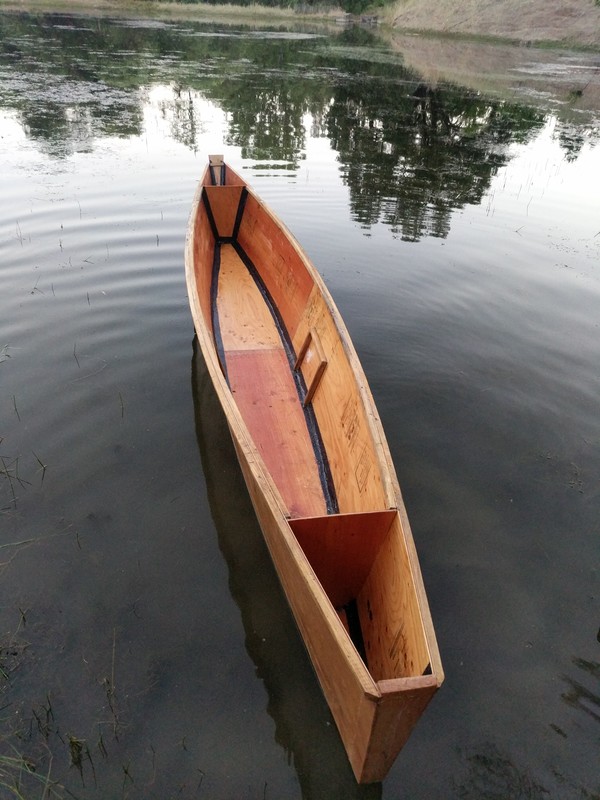
Outrigger shaping
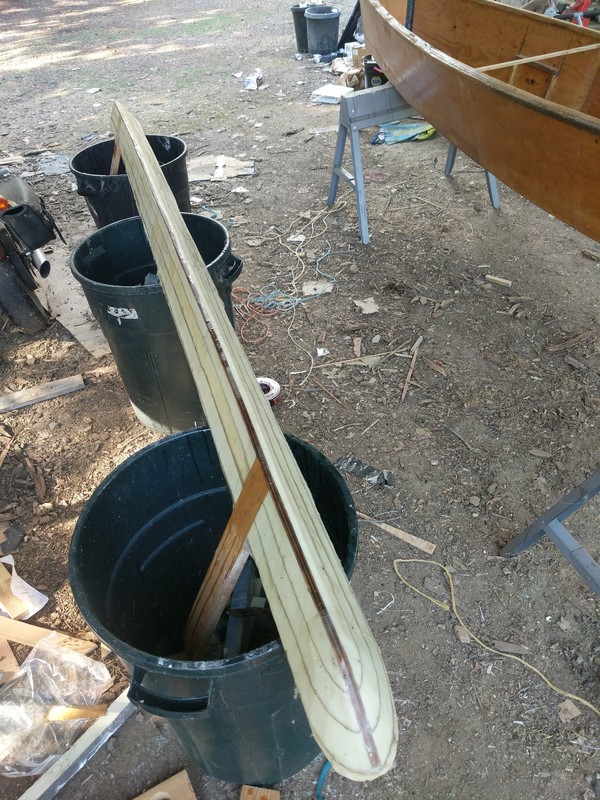
Heyooo birdo!
Measure Hella
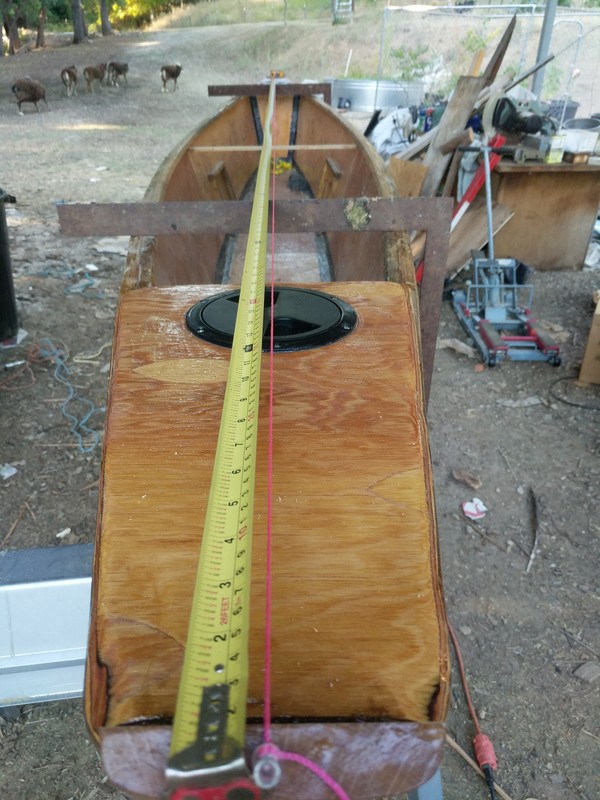
Oh hey, the bulkhead covers are on.
Cut Once
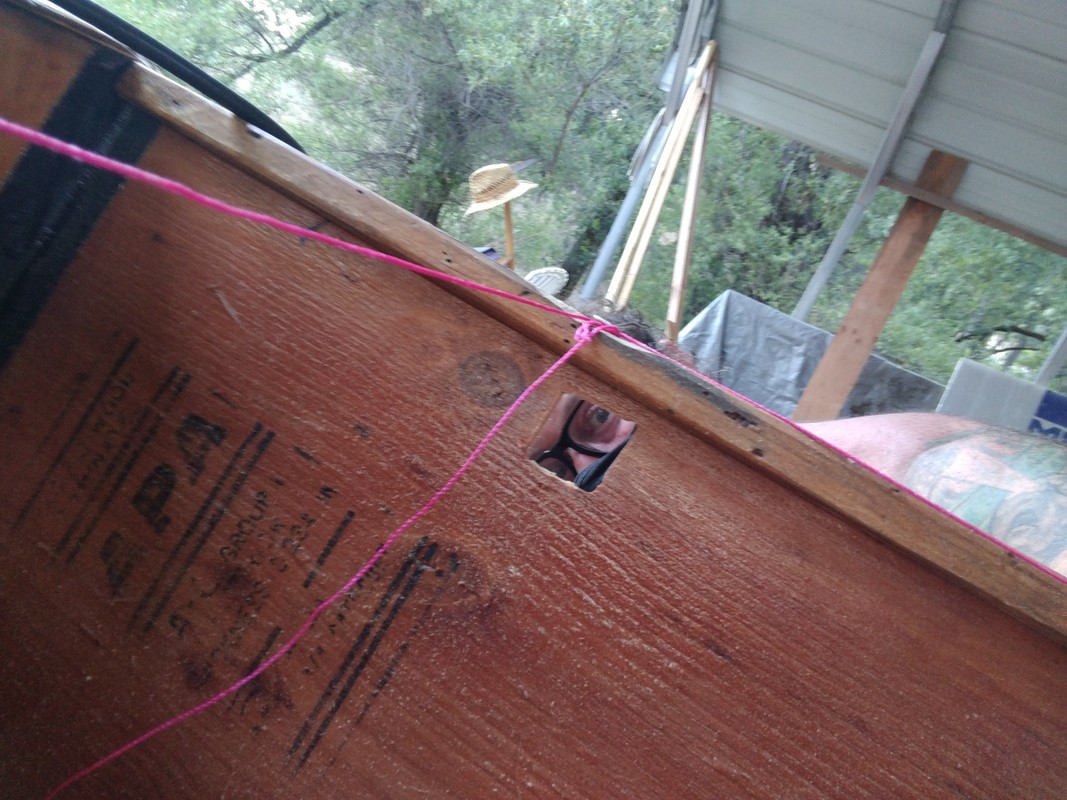
Strut and boom peg
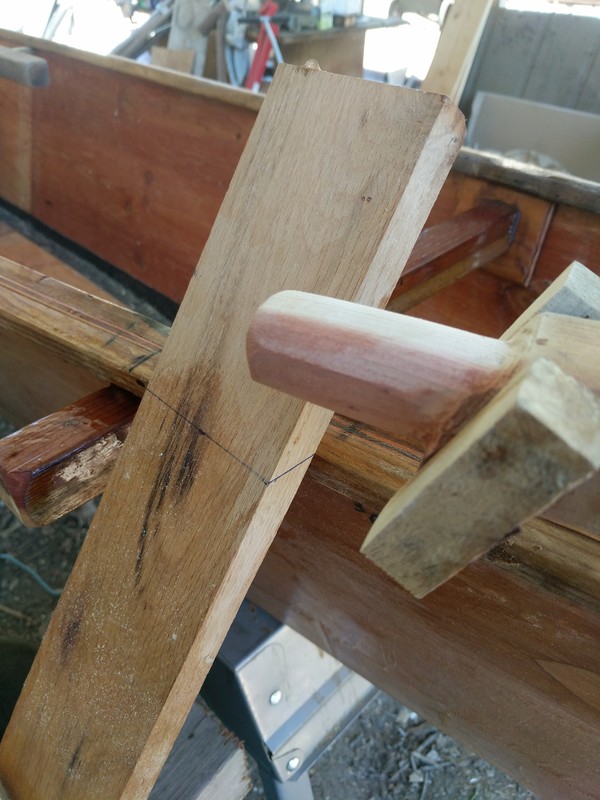
Connected!
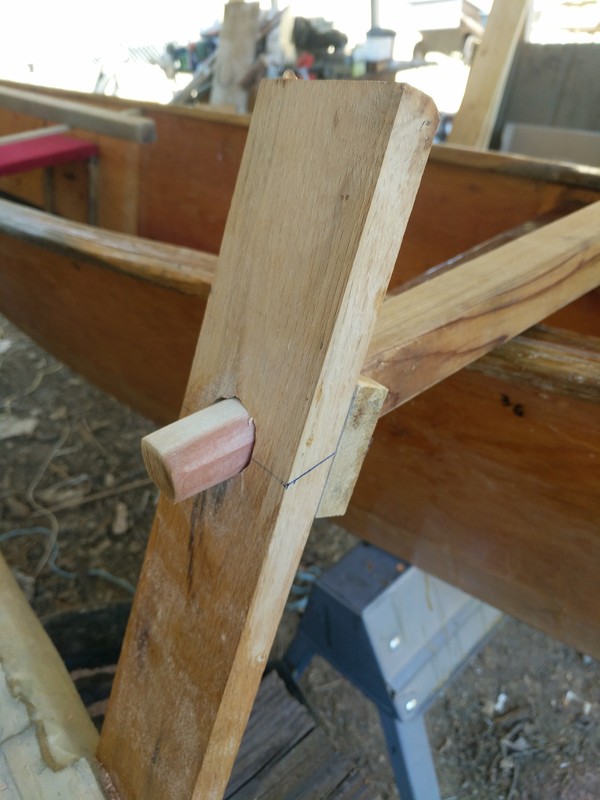
First paddle
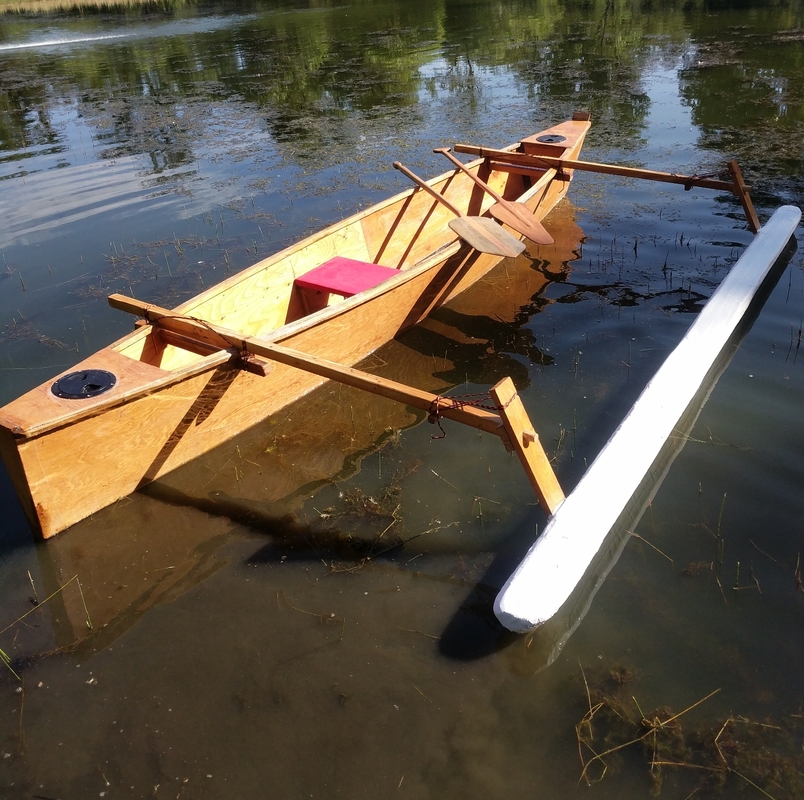
Front strut
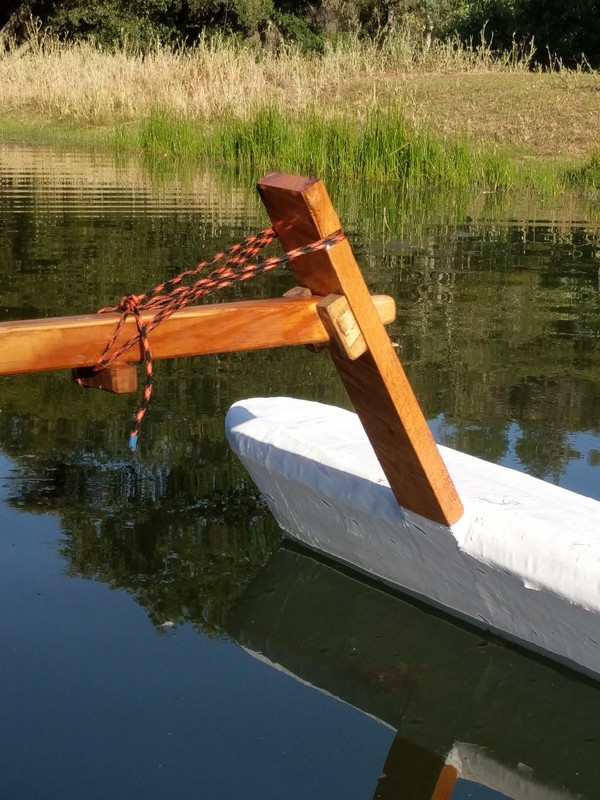
Rear strut
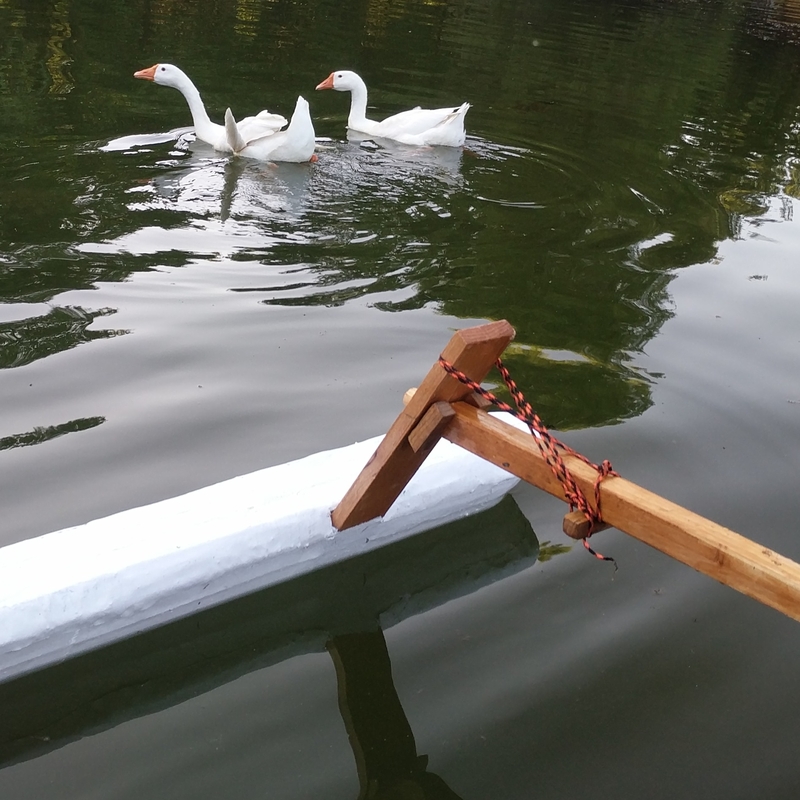
Reflection
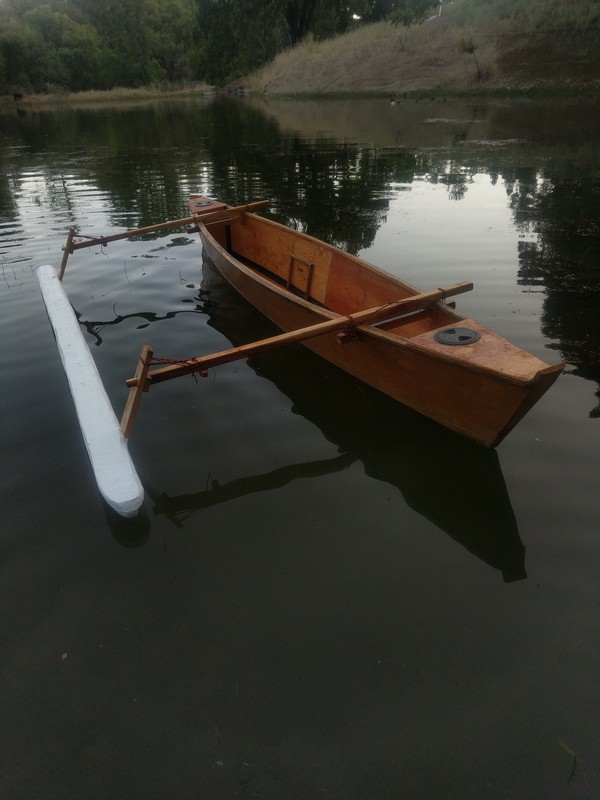
About 30 seconds after launch, the seat crumpled. Crack and I was sitting on a pile of bad engineering. My quest for a thin insanely light seat continues though. A new frame of foolishly thin oak is in the works.
Honestly, I didn't really need that seat. The floatation cushion that I brought along was used as a seat on the floor of the canoe. Aside from sitting, I also tested paddling while kneeling and standing. Kneeling on the cushion while being closer to the bow probably provided the quickest steering. Paddling while standing required squatting a bit to get the paddle blade in the water. It was a fine bit of cardio.
Other than the seat failure, the only other issue encountered was water getting into the aft bulkhead. After I had finished paddling, Woofsnaval spend the night in the water with only the tip of the bow on land. Somehow this resulted in water getting into the bulkhead; either by seeping through the hull or seeping in from the cockpit. The boat was quickly back in the shop for some drying, and some more epoxy.
As of this writing, Woofsnaval has received a coat of paint, and is being prepped for a trip to an actual lake. :)
Cheers,
jezra
edit: the adventure continues…